How can SiC optimize the energy efficiency and performance of hybrid and electric vehicles compared to IGBT?
With increasing interest and market support for electric vehicles (EVs) and hybrid vehicles (HEVs), competition among automakers is becoming increasingly fierce to provide high-quality products to an expanding customer base. Due to the need for high kilowatt hour power supply to drive EV motors, traditional 12 V batteries have given way to battery packs in the order of 400-450 V DC, becoming the mainstream battery voltage for EVs and HEVs.http://www.ic-bom.com/
The market is already pushing for a shift towards higher voltage batteries. 800 V DC and larger batteries will become more advantageous, as using higher voltages means that the system can operate at lower currents while achieving the same power output. The advantages of lower current are lower losses, less heat dissipation to manage, and the use of smaller cables to power the entire vehicle.http://www.ic-bom.com/
The main load of the battery is the vehicle‘s motor, and EV and HEV using AC motors rely on the main drive inverter to convert DC battery power into AC power. The main drive inverter is the heart of an electric vehicle, providing the torque and acceleration required to drive the vehicle forward. The two main design considerations for the main drive inverter include conversion efficiency and peak power.
The higher the efficiency of power conversion from DC to AC, the vehicle can use smaller batteries to do more things. Higher efficiency also means that the system can provide more power and reduce the amount of heat dissipation that needs to be managed.
Peak power determines the overall performance of a vehicle, especially its instantaneous torque and acceleration ability. Efficiency (range) and peak power (performance) jointly determine the application and usage scenarios of vehicles.
Nowadays, many EVs and HEVs are built based on IGBT technology. With the advent of silicon carbide (SiC) technology, higher efficiency and performance have become possible.http://www.ic-bom.com/
Advantages of Silicon Carbide
IGBT technology typically provides more cost-effective solutions for mid to low-end vehicles, while SiC provides excellent efficiency and peak power, especially at higher voltages. It is suitable for vehicles that place great emphasis on range and performance, and the system cost is also more flexible. Each chip has lower impedance, achieving excellent efficiency and thermal optimization. Under the combined action of these functions, the battery consumption per mile is reduced. Although the cost of SiC is higher than that of IGBT, in many applications, this is offset by the cost savings in other aspects of the vehicle brought about by the improved energy efficiency of SiC.
Conversion efficiency:
Essentially, current IGBT technology will become thicker and less efficient with increasing voltage, leading to the need for higher blocking voltage. Higher voltage inverters can be built based on IGBT, but as the voltage of electric vehicles reaches 800 V and above, the efficiency of SiC will be significantly higher than that of IGBT. At higher voltages, SiC does not need to be as thick as IGBT to achieve voltage blocking. Under standard load, the efficiency of IGBT is approximately 94%. However, at lower loads, its efficiency drops to 92%, such as when the vehicle is running at cruising speed. In contrast, SiC can reach 98% under standard load with a gain of 4%. SiC has a 95% efficiency and a gain of 3% at lower loads.http://www.ic-bom.com/
Increase driving distance:
A 100 kilowatt hour battery and IGBT based inverter solution can generate a maximum driving range of 300 miles. Using SiC can increase efficiency by more than 3%, which will increase the vehicle‘s range by 9 miles or more. For vehicles with larger batteries, such as long-distance transport trucks, the range will be longer.
Smaller diameter wiring:
The motor can be driven at a lower current because the SiC based main drive inverter operates more efficiently at higher voltages. This way, smaller diameter cables can be used. The diameter of the wiring that runs through the vehicle has decreased, reducing the overall weight, so that less electricity is needed to drive the vehicle and increase the total driving distance. In addition, smaller diameter wiring costs are lower, offsetting the cost of using high-voltage SiC main drive inverters.http://www.ic-bom.com/
System size:
The efficiency of SiC technology is higher, making the high-voltage main drive inverter more compact in size without affecting efficiency or peak power. The smaller inverter provides designers with greater flexibility in the placement of the inverter and maximizes the passenger and available space inside the vehicle.
Thermal management:
Managing the heat inside the vehicle is crucial for maintaining overall system efficiency. The main drive inverter based on SiC has higher thermal efficiency, which can generate lower losses and less heat dissipation. This means that the inverter operates at lower temperatures, bringing dual benefits: the traction system can achieve higher peak power while reducing the overall cost of the cooling system.
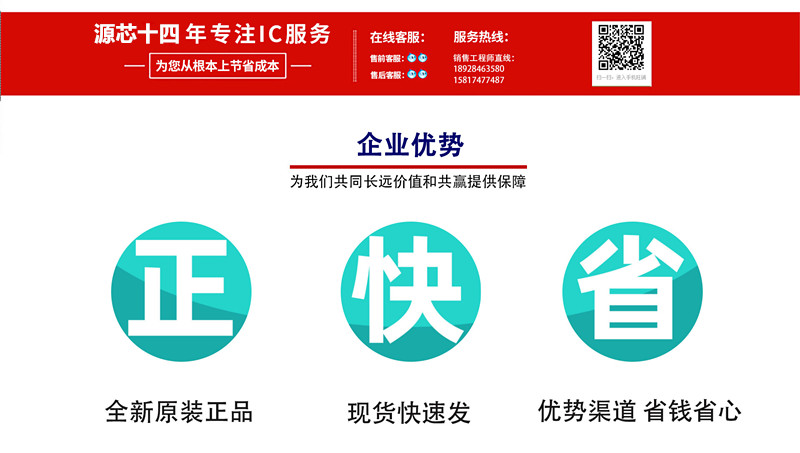