In the wafer manufacturing process, some wafer substrates require further construction of epitaxial layers to facilitate device manufacturing. Typical examples include LED light-emitting devices, which require the preparation of GaAs epitaxial layers on silicon substrates; Grow SiC epitaxial layers on conductive SiC substrates for constructing devices such as SBD and
MOSFET, for power applications such as high voltage and high current; Build a GaN epitaxial layer on a semi insulating SiC substrate to further construct HEMT and other devices for RF applications such as communication. This process cannot be separated from CVD equipment.

In CVD equipment, the substrate cannot be directly placed on metal or simply placed on a certain base for epitaxial deposition, as it involves various influencing factors such as gas flow direction (horizontal and vertical), temperature, pressure, fixation, and detachment of pollutants. Therefore, it is necessary to use a base, then place the substrate on a disk, and then use CVD technology to epitaxial deposit on the substrate. This base is a SiC coated graphite base (also known as a tray).http://www.ic-bom.com/
SiC coated graphite substrates are commonly used as components for supporting and heating single crystal substrates in metal organic chemical vapor deposition (MOCVD) equipment. The thermal stability, thermal uniformity and other performance parameters of SiC coated graphite base play a decisive role in the quality of epitaxial material growth, and therefore are the core and key components of MOCVD equipment.
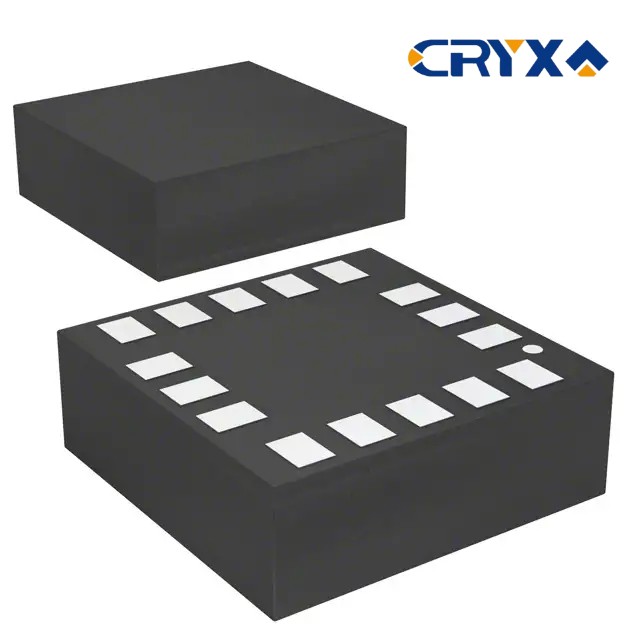
Metal organic chemical vapor deposition (MOCVD) technology is currently the mainstream technology for epitaxial growth of GaN thin films in blue LED, with the advantages of simple operation, controllable growth rate, and high purity of GaN thin films grown. As an important part in the reaction cavity of MOCVD equipment, the bearing base used for GaN film epitaxial growth needs to have the advantages of high temperature resistance, uniform thermal conductivity, good chemical stability, and strong thermal shock resistance. Graphite materials can meet the above conditions.http://www.ic-bom.com/
As one of the core components in MOCVD equipment, graphite base is the carrier and heating element of the substrate substrate, directly determining the uniformity and purity of the thin film material. Therefore, its quality directly affects the preparation of epitaxial wafers. At the same time, as the number of uses increases and the working conditions change, it is also very easy to wear and tear, and belongs to consumables.
Although graphite has excellent thermal conductivity and stability, which gives it great advantages as a base component for MOCVD equipment, during the production process, graphite will corrode and lose powder due to the residual corrosive gases and metal organic matter, and the service life of the graphite base will be greatly reduced. At the same time, falling graphite powder can cause pollution to the chip.
The emergence of coating technology can provide surface powder fixation, enhance thermal conductivity, and balance heat distribution, becoming the main technology to solve this problem. The surface coating of graphite base should meet the following characteristics when used in MOCVD equipment environments:
(1) The graphite base can be fully wrapped and has good density, otherwise the graphite base is prone to corrosion in corrosive gases.http://www.ic-bom.com/
(2) The high bonding strength with the graphite base ensures that the coating is not easily detached after multiple high-temperature and low-temperature cycles.
(3) It has good chemical stability to avoid coating failure in high temperature and corrosive atmosphere.
SiC has the advantages of corrosion resistance, high thermal conductivity, thermal shock resistance, high chemical stability, and can work well in GaN epitaxial atmosphere. In addition, the difference between the coefficient of thermal expansion of SiC and the coefficient of thermal expansion of graphite is very small, so SiC is the preferred material for the surface coating of graphite base.
At present, the common SiC types are mainly 3C, 4H, and 6H, and different crystal forms of SiC have different uses. 4H SiC can manufacture high-power devices; 6H SiC is the most stable and can manufacture optoelectronic devices; 3C-SiC, due to its structural similarity to GaN, can be used to produce GaN epitaxial layers and manufacture SiC-GaN RF devices. 3C-SiC is also commonly referred to as β- SiC, β- One important use of SiC is as a thin film and coating material, therefore, currently β- SiC is the main material used for coating.
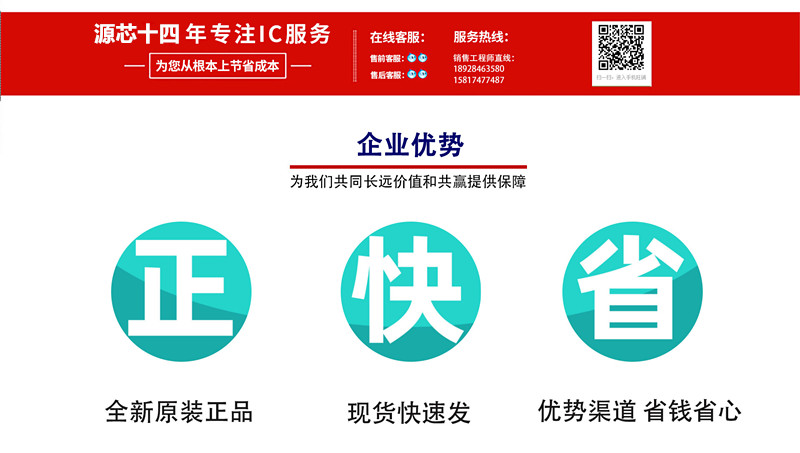